Our research group focuses on materials processing including additive manufacturing (aka 3D printing), testing and characterization of metallic alloys and ceramics for applications that are characterized with “extreme” environment, e.g., temperature, stress, radiation, and their gradients. Our research starts with understanding of microstructure and its development that can be related to processing, properties and performance.
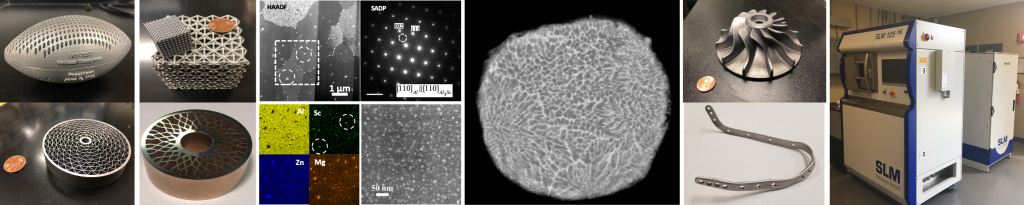
While our topics of research are diverse in applications, our research aims to provide fundamental understanding in microstructure development through thermodynamics and kinetics. Our current emphasis is on metallic alloys, metal matrix composites and protective ceramic coatings for metallic components.
Additive Manufacturing: Powder Processing via Gas Atomization and Laser-Based Powder-Bed Fusion, aka Selective Laser Melting
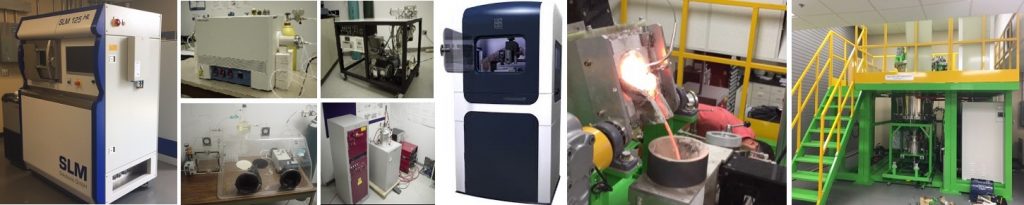
From the ages of stone, bronze and iron, to the advent of steel and semiconductors, the history of civilization can be described in terms of our increasingly sophisticated mastery of new materials. While much of the research focus has been on “new materials” with novel properties, the “sophisticated mastery” (e.g., processing and manufacturing) often has been the rate-limiting step, and in some instances, an insurmountable challenge, in implementing new materials for applications. Advanced manufacturing technology, including additive manufacturing commonly known as 3D printing, is rapidly emerging to provide innovative technology that offers greater processing and manufacturing capability. Once streamlined with a foundation on science, these new manufacturing tools can provide the desired “sophisticated mastery” of new materials concurrently with new materials development.
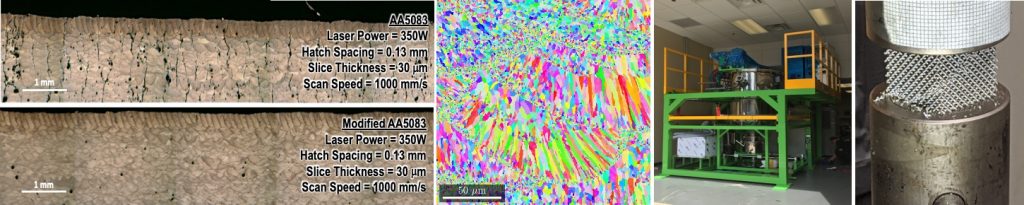
To that end, we have “hands-on-and-closed-loop” capability under “one roof” in additive manufacturing that includes (1) primary metallic powder processing via gas atomization and (2) laser powder-bed fusion (LPBF), commonly known as selective laser melting (SLM 125HL), so that we can design/modify our own metallic alloys to be built (e.g., toner of 3D printing) and optimize LPBF additive manufacturing technology.
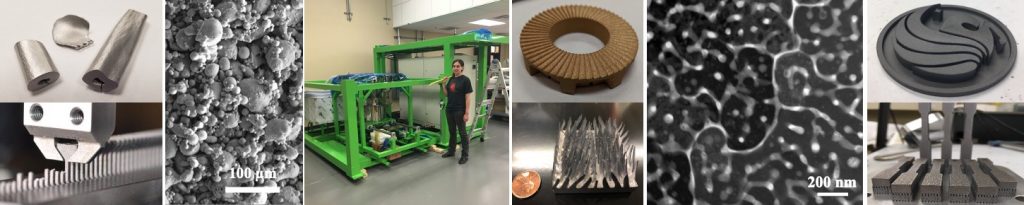
Multicomponent Diffusion under Multiple Gradients
Development of multicomponent alloys also requires control of microstructure through appropriate heat treatments involving solid-state phase transformation and surface modification, where interdiffusion processes play a major role. Diffusion research in multicomponent systems includes experimental, analytical and simulation studies of tracer, impurity, intrinsic diffusion and interdiffusion in metallic alloys and intermetallic phases, diffusion microstructures and diffusion paths in multiphase systems for interface stability, and microstructural evolution kinetic and thermodynamic interactions among the diffusing species.
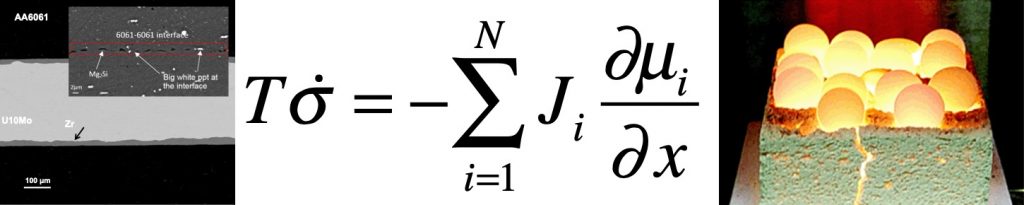
Our experimental and analytical capabilities in multicomponent diffusion can be applied to understand the phenomena of thermotransport and electromigration, in which diffusion occurs due to multiple thermodynamic driving forces including gradients of concentrations (or chemical potential), temperature and electrical potential.
Applications where our knowledge of multicomponent diffusion play an important role includes metallic nuclear fuels alloys (e.g., U-Mo) and coatings for gas turbine applications (e.g., Ni- and Fe-base alloys), multifunctional (e.g., magneto caloric and thermoelectric) alloys and processing of light-weight structural components (e.g., Mg- and Al-alloys).
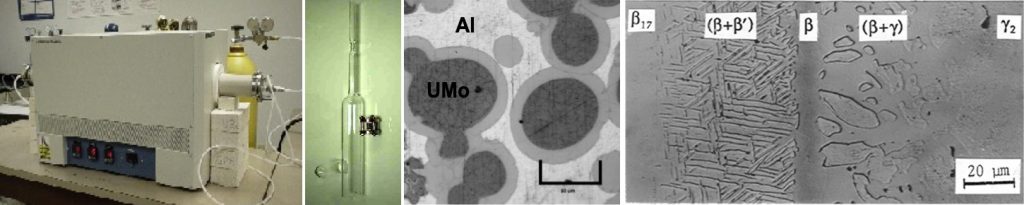
Failure Mechanisms, Non-Destructive Inspection (NDI) Techniques, and Improved Durability/Reliability of Thermal Barrier Coatings (TBCs)
TBCs consisting of ceramic coating, metallic bond coat and superalloy substrate offer thermal protection for hot components in gas turbine engines. Failure of TBCs during cyclic oxidation occurs by spallation near the ceramic/metal interface where thermally grown oxide (TGO) grows due to high temperature oxidation of metallic bond coats. The materials phenomena involved during cyclic oxidation and consequent failure of TBCs are complex, and include phase transformation, sintering, multicomponent diffusion, oxidation, creep, fatigue and fracture. Our research group focuses on an investigation of failure mechanisms for TBCs based on an understanding of these phenomena.
Practical engineering solutions for quality control and life-remain assessment by NDI techniques are important for industrial users of TBCs. Development of NDI techniques such as Photostimulted Luminescence Spectroscopy (PSLS) and Electrochemical Impedance Spectroscopy (EIS) is actively pursued in the light of quality control and life-remain assessment of TBCs. In addition, improvement in durability and reliability of TBCs is being sought through innovative materials design and processing.
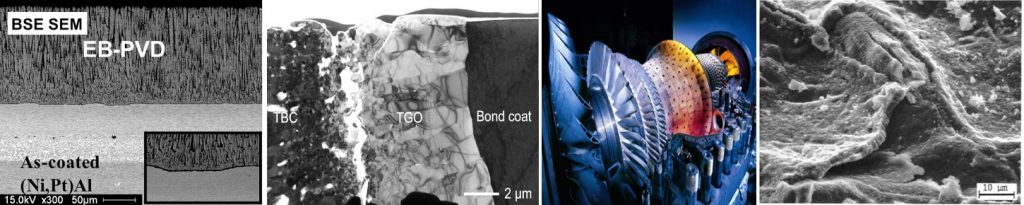
Metal Matrix Composites incoporating Nanostructured Materials
Lightweight metals are generally associated with Al and Mg alloys. To obtain performance beyond that of conventional lightweight metals requires novel processing techniques, to enable these materials to gain greater strength while at the same time reducing weight. This is achieved by forming a composite of ceramic particulates, whiskers and/or fibers within a matrix of aluminum or magnesium. These metal matrix composite (MMC) materials have the potential to achieve the mechanical performance of high-strength steel at one-third the weight. Furthermore, use of nano-grained matrix (Al and Mg) mixed with conventional micro-grained matrix (Al and Mg) can yield “designer” MMCs tailored to specific properties for specific applications. In our group, we examine the process-dependent microstructure and fracture characteristics of Al- and Mg-base MMCs to improve processing-ability and mechanical properties (strength, ductility, impact resistance, etc.).
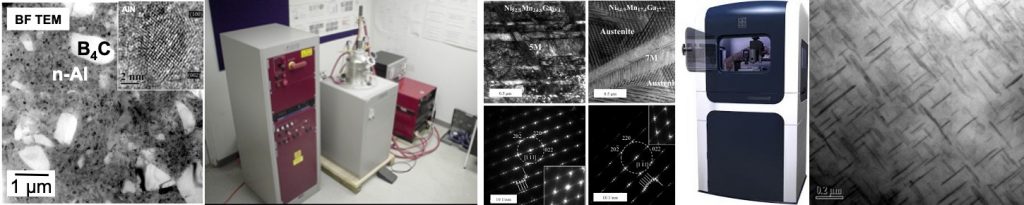